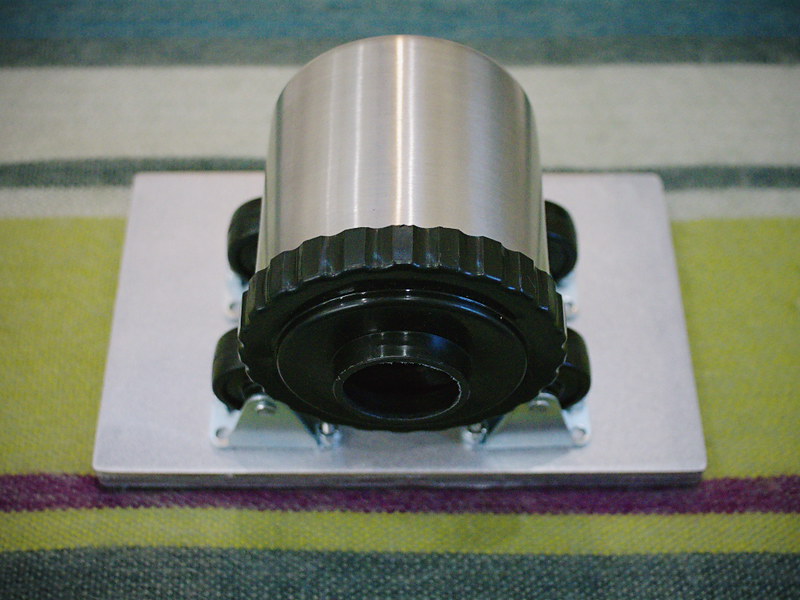
For a few years now, I've been working with the Harman Direct Positive Paper, a silver gelatin, fiber based, black & white print paper that has a direct positive emulsion, meaning that it can be directly exposed inside of a camera to produce, after development using standard chemistry, a one-of-a-kind print. There was a point in time, for about a year, when the paper was out of manufacture, due to a chemical supplier going out of business and another source having to be found, but now it's once again being made, and supplies are plentiful.
I've created one-of-a-kind prints using this medium in a variety of sizes, from sub-miniature Minox-sized to 8"-by-10". While the larger formats require either tray development in a darkroom setting or a large processing drum, and the Minox-sized prints were best handled in small containers in a darkroom, it is in those intermediate-sized formats, from 35mm to 4"-by-5", that I've done most of my work with this paper, and hence would like to find more convenient working methods.
One of the main issues I have is during the winter months, when my unheated, garage-based darkroom requires considerable time to warm up using a space heater, precluding spur-of-the-moment boughts of darkroom creativity. What I'd like is at least a way to work with the Harman paper in the convenience of my kitchen.
While I do have a Jobo processing drum for 4"-by-5" prints, the associated manual roller base is a rather pricey and fragile item. However, for smaller-sized prints - such as those cut to custom sizes for loading, one-at-a-time, into small and medium format cameras - there is no custom-fit processing tank available.
Several years ago, in a fit of inspiration, I decided that I might be able to use a stainless steel 35mm developing tank as a makeshift rotary processor for these special-sized smaller prints. The idea was that the reels would be kept inside the tank and the paper would be slipped into the gap between the outside of the reels and the inner surface of the tank, with the emulsion facing inward. With the lid installed, an adequate quantity of chemicals - about 100mL - can be used for processing without sloshes spilling from the lid, as the tank is oriented sideways and continuously rotated.
What I needed to make this work was a roller base. I had the Jobo base for my larger formats, and I figured out how to rearrange the roller brackets to make it work somewhat for the smaller steel tank, but I wanted a dedicated solution, so I wouldn't have to keep re-configuring the Jobo roller base; it being made of plastic, I was concerned the pieces would eventually break.
And so last week I went to the hardware store and looked for some caster wheels. I noticed there were three kinds, two of which were unusable because the wheels swiveled on bearings. I wanted wheels that rolled on a fixed support mount but didn't swivel. I found what I was looking for, and went immediately to my workshop to begin fashioning the roller base.
I first had to figure out how to properly space the four wheels. So I used an old scrap piece of plywood as a test base and, using clamps, tried various configurations with the wheels and steel tank until I found an optimal configuration where the tank easily rolled on the wheels. I then measured the positions of the wheel brackets and transferred those measurements to the nice piece of plywood, that I had prepared ahead of time by spray painting a metallic silver color.
I countersunk flathead screws through the bottom of the base, with the holes tapped to fit, and used nylon locking nuts to secure the wheels. The bottom I covered in a sheet of rubber matting material via a hot glue gun, making for a nonskid, water-resistant surface.
The result is a roller base custom fitted to my stainless steel developing tank, with which I can continue in earnest creating more small-gauge, silver gelatin, direct positive prints.
I also created a video about this project, which I encourage you to watch.
I've always been intrigued by small-format black & white prints. I can recall a time, about 15 years ago, when I saw an exhibit of Edward Weston prints at the Portland Art Museum. I was absolutely stunned by the quality of the work, the physical appearance of the prints and their intimate, diminutive size. You needed to get in close to them, in order to properly appreciate their beauty. In turn, that physical intimacy allowed one to perceive them as real objects, with real physical attributes such as surface finish and tone, rather than mere image files.
I believe in this age of media over-saturation that we need to reconnect to the tangible reality of the physical art object itself. Direct positive prints, made on a gallery-quality substrate of Ilford's best double-weight, fiber-based photographic paper, represent just such a medium, ripe for further exploration.
I'm hoping that projects such as these will provide you with the inspiration and tools necessary for you to pursue your own exploration of the world of direct positive photographic prints. I'd like to hear about you work, so leave a comment if you can.
No comments:
Post a Comment
Please leave a comment; I will curate them before posting.